Network Visibility Products
Garland Technology ensures complete packet visibility by delivering a full platform of network TAP (test access point), inline bypass and packet broker products.
Visibility Solutions
Garland Technology is committed to educating the benefits of having a strong foundation of network visibility and access. By providing this insight we protect the security of data across your network and beyond.
Resources
Garland Technology's resource library offers free use of white papers, eBooks, use cases, infographics, data sheets, video demos and more.
Blog
The TAP into Technology blog provides the latest news and insights on network access and visibility, including: network security, network monitoring and appliance connectivity and guest blogs from Industry experts and technology partners
Partners
Our extensive technology partnership ecosystem solves critical problems when it comes to network security, monitoring, application analysis, forensics and packet inspection.
Company
Garland Technology is dedicated to high standards in quality and reliability, while delivering the greatest economical solutions for enterprise, service providers, and government agencies worldwide.
Contact
Whether you are ready to make a network TAP your foundation of visibility or just have questions, please contact us. Ask us about the Garland Difference!
How Manufacturers Gain Full Visibility in OT While Adopting Industrial IoT Technologies
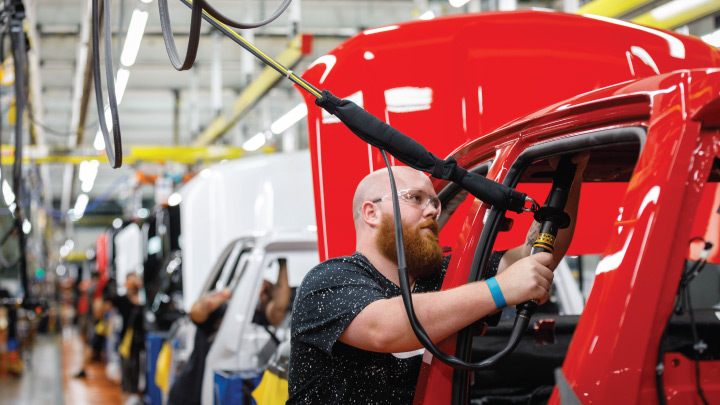
Etymologically speaking, the word “manufacturing” has its roots in a Latin phrase that means “making by hand.” In practical terms, when talking about manufacturing, you're talking about factories – that is, non-residential facilities that use powered machines to help humans turn out goods for some sort of business enterprise. You may also be thinking about industries – that is, the manufacturing of distinct types of goods such as automobiles, aerospace, electronics, chemicals, pharmaceuticals, and so on.
If you’re directly involved in industry, you also understand that manufacturing involves more than machine production. It also encompasses the machines themselves, plus the processes and systems used to control and monitor the performance of the machines.
In other words, it means operational technology (OT). And within the last decade, OT has come to include connected monitors and sensors as well as mechanical and digital equipment, processes and systems. The term now covers the use of industrial internet of things (IIoT) devices in industrial control systems (ICS) and the manufacturing equipment itself.
It seems fair to say, then, that the word “manufacturing” has experienced a certain amount of mission creep. That is, it’s gone from describing the making of goods by hand to describing complex physical structures and processes that use mechanical, digital and connected equipment powered by electricity to turn out goods for distribution and sale.
Connected Systems are an Increasingly Important Aspect of Modern Manufacturing
But mission creep isn’t necessarily a bad thing – especially not when the use of IIoT devices has been expanding exponentially in recent years and is set to continue doing so.
Million Insights predicted in a report published in 2019 that the value of the global IIoT market would reach US$922.62 billion by 2025, up from almost nothing 20 years ago, and this figure may prove to be overly conservative. The coronavirus (COVID-19) pandemic has given manufacturers new reasons to adopt connected systems by creating incentives for remote monitoring and control, and major technology providers such as Microsoft have responded by expanding their involvement in IIoT solutions.
What’s driving this expansion is the fact that connected monitors and sensors have the potential to save costs and add value to manufacturing in a variety of ways, including but not limited to improvements in safety, predictive and preventative maintenance, more accurate tracking of personnel and inventory, and updating of legacy systems and equipment. According to a study published last year by McKinsey, IIoT applications have the potential to generate an additional US$1.2-3.7 billion worth of value by 2025.
IIoT Applications Can Add Value – If They’re Adequately Secured
That added value won’t be a given, though. It will have to be secured.
And that’s because connected systems bring risks as well as rewards. Every point of connection – every monitor, every sensor, every terminal, every remote access option, every patch installed on legacy devices, every link to corporate information technology (IT) systems, every server set up to run the system – has some degree of vulnerability to cyberattacks.
Manufacturers must work to minimize this risk. If they don’t, they could fall victim to malware or ransomware attacks, which cause business continuity to be lost, production interrupted, equipment damaged, and/or raw materials wasted, resulting in billions of dollars in losses and clean-up costs.
They could also leave themselves open to corporate espionage incidents involving the loss of intellectual property, trade secrets, and/or proprietary formulas, designs, and processes via connected devices – and this isn’t just a theoretical risk. Verizon’s Cyber-Espionage Report, published last November, concluded that attacks on manufacturers account for 22% of all cyberespionage incidents, second only to the public sector at 31%.
Making Visibility Part of the OT Security Strategy
So how can manufacturers avoid such negative consequences?
It helps to adopt policies that recognize the risk from the outset. If you’re looking to bring new IIoT systems online at your facilities, you should also look for cybersecurity services at the same time. Make cybersecurity part of the procurement process.
Alternatively, if you already have IIoT solutions in place and want to safeguard them, bear in mind that there are often gaps between IT security and OT security. These gaps may arise from the fact that legacy OT systems may lack appropriate traffic aggregation systems or require uni-directional connectivity. They may also stem from differences in speed or media connections or reliance on switch SPAN ports that aren’t secure, reliable, or available.
To identify potential problems ahead of time, you’ll need to conduct vulnerability assessments, and you’ll need to conduct them repeatedly and regularly so that you can prioritize the mitigation of attack paths to critical assets and procedures. Currently, manufacturers simply don’t do enough of this. According to CyberX, 31% of manufacturers have never carried out any vulnerability assessments at all, while 50% do so only occasionally.
You’ll also need to make sure that your cybersecurity solutions offer operational visibility because you can’t secure what you can’t see.
It’s a fundamental best practice in the cybersecurity arena to have a system inventory of all the networked devices and ICS being monitored so that users can determine what facilities are connected to their networks and who is active on their networks. Visibility solutions will support this best practice by giving manufacturers’ cybersecurity teams comprehensive visual representations of the information they need and identifying the sources of the information.
In turn, visibility solutions should always entail the implementation of fundamental best practices in visibility architecture. You can achieve this by eliminating blind spots in your network so that ICS security tools can detect threats and anomalies and carry out continuous monitoring. You’ll need to make sure that your tools can carry out complete analyses of packet data visibility – and for that, you’ll need to deploy network TAPs, air-gapped virtual TAPs, and data diodes with your security and infrastructure strategy.
Looking to add visibility to your manufacturing environment, but not sure where to start? Try joining us for a brief network Design-IT consultation or demo. No obligation - it’s what we love to do.
Written by Ross Green
Ross is the European Sales Director for Garland Technology with over 30 years experience in the networking & security industry. Ross's experience spans computer/network engineering, consultancy, sales and senior EMEA business management roles.
Authors
Topics
- IT Security (201)
- Network TAPs (139)
- Network Monitoring (135)
- Hacks and Breaches (87)
- Network Management (81)
- Network Design (73)
- Industrial OT (71)
- Technology Partners (63)
- Network Infrastructure (59)
- Inline Security (50)
- TAPs vs SPAN (47)
- Network Packet Brokers (41)
- Data Center (37)
- Cloud Solutions (33)
- Software Defined Networking (SDN) (24)
- Events & News (20)
- The 101 Series (19)
- Federal (17)
- Cisco Solutions (16)
- Wireshark (14)
- DesignIT (13)
- Healthcare (11)
- MSP/MSSP (9)
- Palo Alto Networks (8)
- Finance (7)
- Troubleshooting (5)